Mastering Finite Scheduling: Strategies for Optimal Resource Management
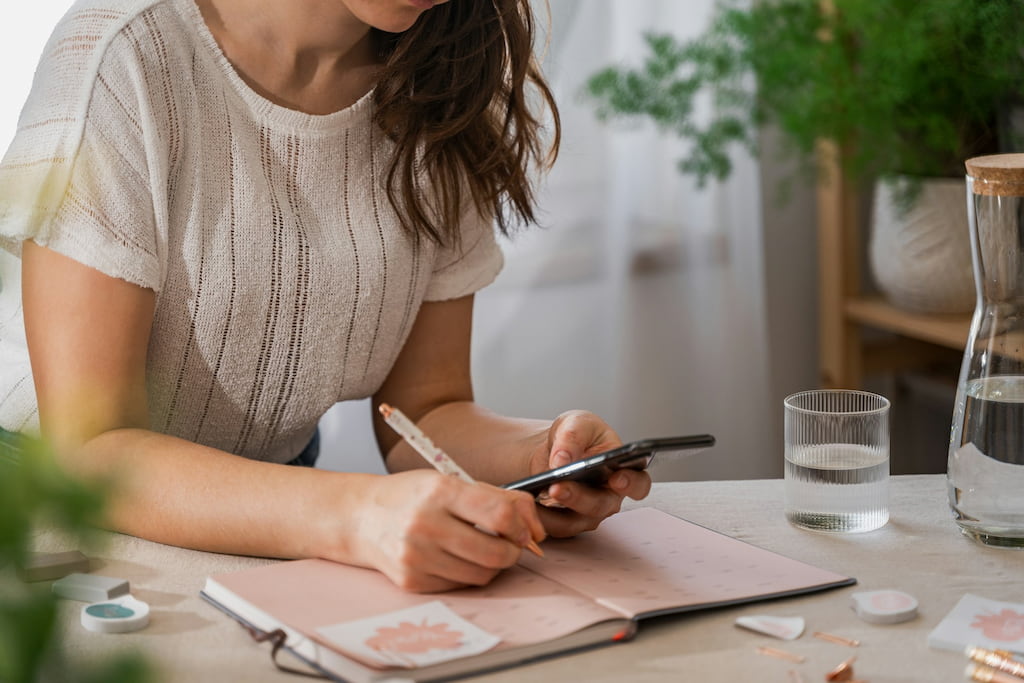
Finite scheduling is a critical component of effective project and resource management, particularly in environments where resources are limited and demand is high. Unlike infinite capacity scheduling, which assumes unlimited resources and time, finite capacity scheduling takes into account the actual constraints of resources, ensuring that tasks are scheduled based on real-world availability. This method helps organizations optimize their workflows, minimize bottlenecks, and enhance overall efficiency. By understanding and implementing finite scheduling, businesses can better allocate their resources, meet deadlines, and improve productivity.
What is Finite Scheduling?
Finite scheduling is a method used in production and project management to allocate resources and schedule tasks based on the actual limitations of available resources.
Unlike infinite capacity planning, which assumes unlimited resources, finite scheduling and capacity planning take into account the real-world constraints of equipment, labor, and materials.
🌟 Key aspects of finite capacity planning
- Resource constraints: Finite capacity planning considers the availability of resources such as machinery, workforce, and materials. It ensures that tasks are scheduled based on the actual capacity of these resources, preventing overallocation and bottlenecks.
- Realistic scheduling: By acknowledging the limitations of resources, finite capacity planning creates more realistic schedules. This leads to more accurate timelines for project completion and helps in setting achievable deadlines.
- Prioritization and optimization: This planning method allows for the prioritization of tasks based on their importance and urgency. It optimizes the use of resources by ensuring they are allocated to the most critical tasks first, improving overall efficiency.
- Bottleneck management: Finite capacity planning helps identify potential bottlenecks in the production process. By addressing these constraints proactively, organizations can minimize delays and ensure a smoother workflow.
- Flexibility and adaptability: With a finite capacity plan, organizations can quickly adapt to changes in resource availability or project requirements. This flexibility is crucial in dynamic environments where unexpected issues or changes in demand can occur.
- Improved productivity: By aligning resource availability with project demands, finite capacity planning enhances productivity. It ensures that resources are not sitting idle or overburdened, leading to a more balanced and efficient operation.
❗ Note: In general, finite scheduling and finite capacity planning are closely related concepts but entail distinct focuses within the realm of resource management. While both concepts aim to optimize resource utilization, finite scheduling emphasizes the scheduling aspect, whereas finite capacity planning encompasses broader strategies for managing resources within defined constraints. In this article, however, they’ll be interchangeable.
➡️ Shifts by Everhour provides an intuitive shift scheduling software for managing employee schedules with ease. From flexible scheduling options to mobile accessibility, it’s the ideal solution for optimizing workforce management in any industry.
Importance of Finite Scheduling & Capacity Planning
📅 Accurate timelines: Finite scheduling considers actual resource capacity, leading to reliable timelines and realistic deadlines.
🔧 Resource optimization: It ensures optimal use of labor, machinery, and materials, preventing overallocation and underutilization.
🚦 Bottleneck prevention: By identifying and addressing potential bottlenecks in advance, it minimizes delays and disruptions.
💸 Cost efficiency: Efficient resource use reduces waste and expenses, maximizing return on investment.
🚀 Improved productivity: Tasks are planned based on actual capacity, streamlining processes and reducing idle time.
🔄 Enhanced flexibility: Allows adjustments to changes in resource availability or project requirements, enabling quick responses to challenges.
📊 Better decision-making: Provides a realistic view of resource availability and task timelines, supporting informed decision-making.
🤝 Customer satisfaction: Helps meet deadlines and deliver projects on time, enhancing customer relationships and reputation.
⚠️ Risk management: Early identification of constraints allows proactive risk management, reducing project delays.
How to Develop a Capacity Strategy
When formulating a finite capacity strategy, it’s important to consider several key factors to ensure optimal resource utilization and efficiency. Here are the essential steps:
- Assess current capacity: Evaluate existing resources, including labor, equipment, and materials. Understand the maximum achievable output.
- Analyze demand: Study historical data and market trends to predict future demand, considering seasonal fluctuations and market growth.
- Identify capacity gaps: Compare current capacity with projected demand to spot gaps. Determine if there’s a need to boost capacity.
- Set capacity goals: Establish measurable goals for capacity expansion that align with your organization’s business strategy.
- Develop a capacity expansion plan: Create a detailed plan, possibly involving new equipment, staff, or process improvements.
- Leverage data and analytics: Use data analytics to gain insights into capacity utilization and demand patterns for more accurate predictions.
How to Create and Implement a Finite Capacity Plan
Creating and implementing a finite capacity plan involves several key steps. Here’s a detailed guide to help you through the process:
Define objectives
- Clearly outline the goals of your finite capacity plan.
- Align these goals with your overall business objectives.
Gather data
- Collect accurate data on current capacity, resource availability, and production schedules.
- Ensure data is comprehensive and up-to-date.
Analyze resource constraints
- Identify any constraints in resources like equipment, labor, or materials.
- Understand how these constraints affect your production capacity.
Develop a baseline schedule
- Create a schedule that reflects your current production capabilities.
- Consider all known constraints and available resources.
Incorporate buffer times
- Add buffer times to account for potential delays or issues.
- Ensure the plan is realistic and achievable under normal conditions.
Optimize resource allocation
- Allocate resources efficiently to maximize productivity.
- Use scheduling tools to assign tasks based on availability.
Use advanced planning tools
- Implement advanced planning and scheduling (APS) tools.
- These tools help balance workloads and minimize bottlenecks.
Simulate scenarios
- Run various what-if scenarios to evaluate different impacts on your capacity plan.
- Identify potential risks and develop mitigation strategies.
Collaborate with teams
- Involve key stakeholders in the planning process.
- Ensure the plan is comprehensive and considers all critical inputs.
Create a detailed action plan
- Outline the steps needed to implement your finite capacity plan.
- Include timelines, responsibilities, and specific tasks.
Implement the plan
- Roll out the plan across the organization.
- Ensure all teams are informed and understand their roles.
Monitor progress
- Continuously track the implementation of the plan.
- Monitor key performance indicators (KPIs) to assess progress.
Adjust as needed
- Be prepared to make adjustments based on real-time data and feedback.
- Address any issues promptly to keep the plan on track.
Review and improve
- Regularly review the effectiveness of the plan.
- Gather feedback and analyze performance data to identify improvements.
Document processes
- Document all processes related to the capacity plan.
- Maintain consistency and provide a reference for future planning activities.
By following these steps, organizations can create and implement a finite capacity plan that optimizes resource utilization, improves production efficiency, and supports overall business goals.
Different Types of Finite Capacity Planning
Finite capacity planning involves various approaches to effectively manage and utilize limited resources:
1. Forward scheduling
- ✍️ Description: In forward scheduling, planning begins from the current date and moves forward. This method schedules tasks as early as possible.
- Use case: Best for projects where the start date is flexible, but the finish date must be controlled.
- Advantages: Helps in identifying the earliest completion time and is useful for planning new projects.
- Disadvantages: May result in idle time for resources and less optimal use of capacity.
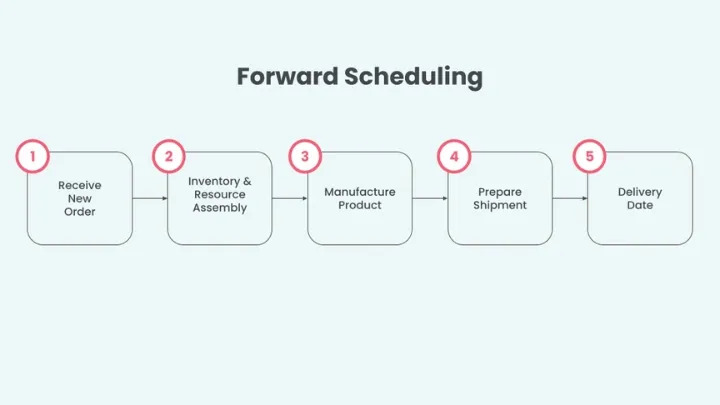
2. Backward scheduling
- ✍️ Description: Backward scheduling starts from the due date and plans tasks backward. The aim is to complete tasks just in time for the deadline.
- Use case: Ideal for projects with fixed deadlines and tight schedules.
- Advantages: Minimizes inventory costs and idle time, ensuring timely delivery.
- Disadvantages: Less flexibility in handling delays and requires accurate estimation of task durations.
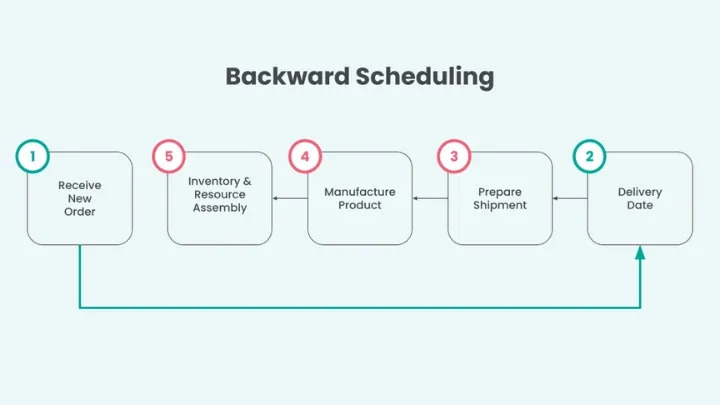
3. Constraint-based scheduling
- ✍️ Description: This method focuses on identifying and managing constraints (bottlenecks) within the production process.
- ❓ Use case: Useful in complex production environments with multiple constraints.
- ✅ Advantages: Optimizes resource use and improves overall efficiency by focusing on critical constraints.
- ❌ Disadvantages: Requires detailed analysis and constant monitoring of constraints.
4. Capacity requirement planning (CRP)
- ✍️ Description: CRP calculates the capacity needed at each work center to meet the production schedule.
- ❓ Use case: Effective in manufacturing environments where resource load needs to be balanced.
- ✅ Advantages: Provides a detailed view of capacity requirements and helps in balancing workload.
- ❌ Disadvantages: Can be complex to implement and requires accurate data.
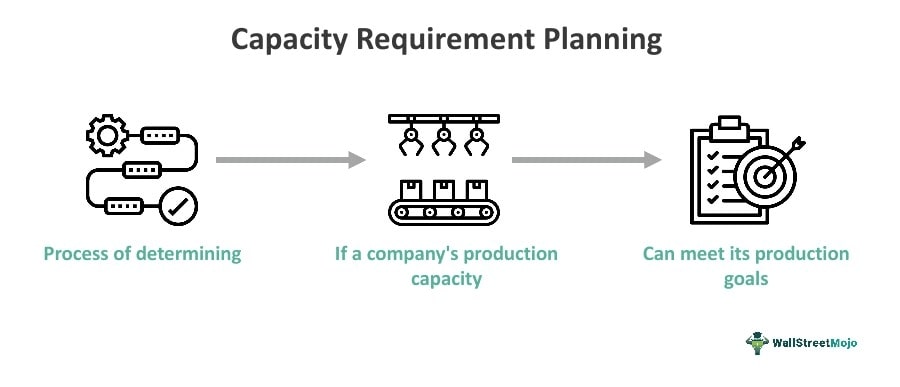
5. Drum-buffer-rope (DBR)
- ✍️ Description: DBR is based on the Theory of Constraints and focuses on scheduling around the system’s constraint (drum), protecting it with a buffer, and synchronizing other resources (rope).
- ❓ Use case: Best for environments with a clear bottleneck that controls the overall flow.
- ✅ Advantages: Enhances throughput and reduces lead times by focusing on the constraint.
- ❌ Disadvantages: May not be effective in environments with multiple shifting constraints.
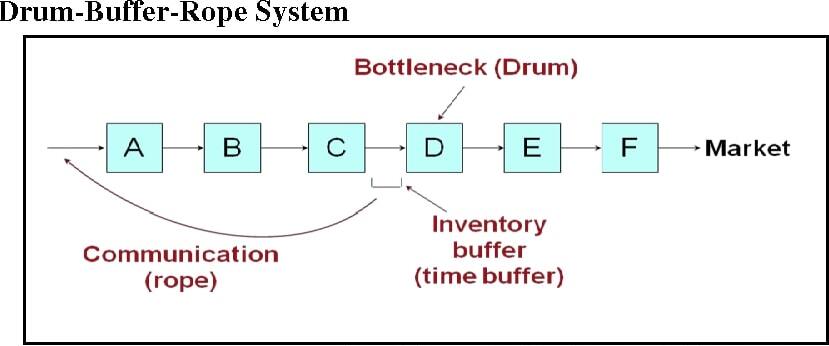
6. Advanced planning and scheduling (APS)
- ✍️ Description: APS systems use sophisticated algorithms to optimize the scheduling of tasks considering multiple constraints and variables.
- ❓ Use case: Suitable for complex manufacturing environments with numerous interdependencies.
- ✅ Advantages: Offers high levels of optimization and flexibility, handling complex scenarios.
- ❌ Disadvantages: Can be expensive and require significant IT resources and expertise.
7. Just-in-time (JIT) scheduling
- ✍️ Description: JIT scheduling focuses on producing goods just in time to meet customer demand, minimizing inventory levels.
- ❓ Use case: Effective in environments where reducing inventory costs and lead times is critical.
- ✅ Advantages: Reduces inventory carrying costs and waste, improving cash flow.
- ❌ Disadvantages: Requires highly reliable processes and supplier relationships.
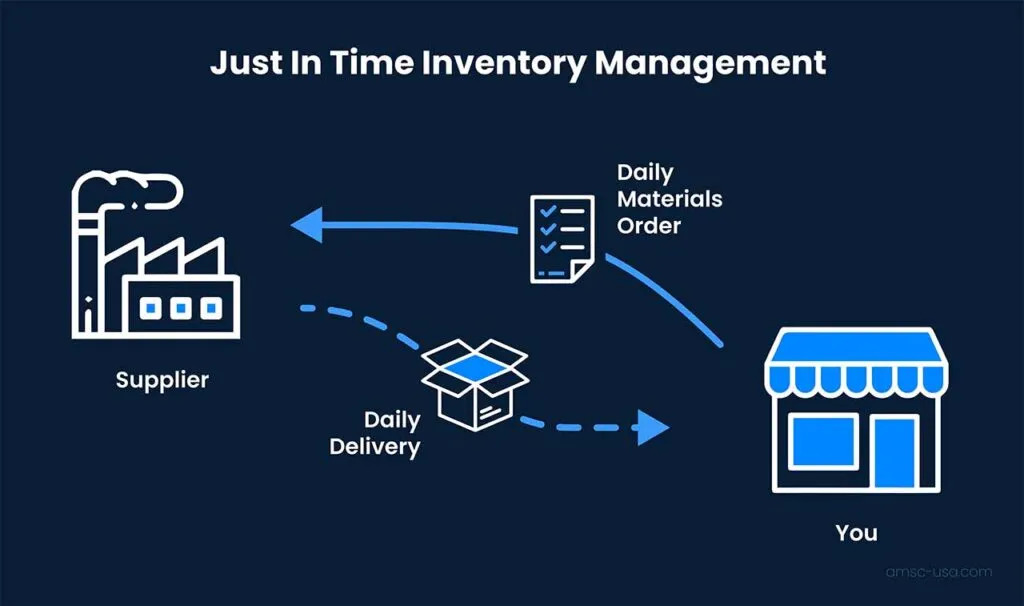
Best Practices for Effective Finite Capacity Planning
To ensure successful implementation and utilization of finite capacity planning, consider the following best practices:
1️⃣ Understanding capacity limits
- Assess current capacity regularly to identify constraints and bottlenecks.
- Implement measures to address and alleviate constraints hindering capacity utilization.
2️⃣ Utilizing advanced planning tools
- Leverage specialized software for advanced planning and scheduling to manage complex scenarios efficiently.
- Integrate planning tools with existing systems to streamline data flow and enhance decision-making.
3️⃣ Maintaining accurate data
- Collect real-time data on production performance, resource availability, and work progress.
- Regularly validate data accuracy to ensure reliability in planning and decision-making processes.
4️⃣ Conducting regular capacity reviews
- Monitor resource performance continuously and compare it against planned capacity.
- Adjust capacity plans based on actual performance and emerging trends to maintain alignment with production goals.
5️⃣ Implementing realistic scheduling
- Create schedules that realistically reflect the available capacity and expected workload.
- Include buffers for unexpected delays and variability in the production process to mitigate risks.
6️⃣ Fostering cross-functional collaboration
- Promote communication and collaboration between departments involved in capacity planning and execution.
- Align goals and objectives across different functions to ensure coherence and synergy in capacity planning efforts.
7️⃣ Optimizing inventory management
- Maintain optimal inventory levels to support production without overstocking or causing delays.
- Implement just-in-time (JIT) principles to minimize inventory costs and improve cash flow.
8️⃣ Providing ongoing training
- Offer training and development programs to ensure staff are proficient in using planning tools and understanding capacity planning principles.
- Encourage continuous learning to keep up with evolving best practices and technologies.
9️⃣ Reviewing and improving processes
- Conduct regular audits of capacity planning processes to identify areas for improvement and optimization.
- Foster a culture of continuous improvement by incorporating feedback and performance data into planning processes.
Challenges of Finite Capacity Planning
Finite capacity planning, while beneficial for optimizing resource utilization and production efficiency, comes with its set of challenges. These are some common challenges faced in implementing and managing finite capacity planning:
Complexity of production processes
Many production environments are inherently complex, with multiple interdependent processes and variables. Managing and coordinating these processes effectively can be challenging, especially when capacity constraints are involved.
Data accuracy and availability
Finite capacity planning relies heavily on accurate and up-to-date data on resource availability, production schedules, and demand forecasts. However, obtaining and maintaining such data can be difficult, leading to inaccuracies and uncertainties in planning.
Dynamic and uncertain demand
Fluctuations in demand for products or services can pose significant challenges to capacity planning. Predicting future demand accurately and adjusting production capacity accordingly is a delicate balance, especially in industries with highly variable demand patterns.
Synchronization of operations
Coordinating multiple production activities and processes to ensure smooth workflow and minimize idle time is essential for efficient capacity utilization. However, achieving synchronization across different departments or functions can be challenging, particularly in large and complex organizations.
Change management and adaptability
Implementing finite capacity planning often requires changes to existing processes, systems, and organizational structures. Resistance to change, lack of buy-in from stakeholders, and difficulties in adapting to new ways of working can impede successful implementation.
Software limitations and integration issues
While specialized software tools can aid in capacity planning, they may have limitations in handling complex scenarios or integrating with existing systems. Compatibility issues, data silos, and lack of interoperability between different software platforms can hinder effective planning and decision-making.
Balancing efficiency and flexibility
Striking the right balance between maximizing resource utilization and maintaining flexibility to respond to changing conditions is a constant challenge in capacity planning. Over-optimization can lead to rigidity and inflexibility, while excessive flexibility may sacrifice efficiency and productivity.
Long-term planning and strategic alignment
Aligning capacity planning efforts with long-term strategic goals and objectives requires foresight, coordination, and alignment across the organization. However, competing priorities, shifting market conditions, and evolving business strategies can complicate long-term planning efforts.
External factors and market volatility
External factors such as economic conditions, regulatory changes, and geopolitical events can impact demand, supply chains, and production operations. Anticipating and mitigating the effects of these external factors on capacity planning requires agility and proactive risk management.
Continuous improvement and adaptation
Capacity planning is an iterative process that requires continuous monitoring, evaluation, and adaptation. Failing to regularly review and adjust capacity plans in response to changing conditions can lead to inefficiencies, missed opportunities, and competitive disadvantages.
Addressing these challenges requires a holistic approach that encompasses people, processes, and technology. By recognizing and proactively addressing these challenges, organizations can enhance their capacity planning capabilities and achieve greater operational efficiency and effectiveness.
Finite Scheduling: Conclusion
By implementing a finite capacity planning approach, organizations can better align their production capabilities with demand, reduce lead times, and enhance overall productivity. However, it’s crucial to recognize and address the challenges associated with capacity planning, such as complex production processes, dynamic demand patterns, and resource constraints.
By leveraging Shifts by Everhour and adopting best practices for capacity planning, organizations can overcome challenges, drive continuous improvement, and achieve greater success in today’s dynamic business environment. With the right tools and strategies in place, organizations can unlock new opportunities for growth, innovation, and competitive advantage.