As organizations operate around the clock to meet the demands of our 24/7 world, finding the right shift pattern becomes a strategic imperative. One shift schedule that has gained prominence in industries requiring continuous operations, such as manufacturing, healthcare, and public safety, is the DuPont schedule. Named after the DuPont Corporation, which pioneered its use in the early 20th century, this scheduling system is designed to ensure that employees maintain a balance between work and personal life while maximizing operational continuity.
In this article, we will delve into the DuPont work schedule, exploring its origins, how it works, and why it remains a preferred choice for certain sectors. Whether you’re an HR manager seeking the ideal shift schedule or an employee curious about the logistics behind your work hours, this guide aims to shed light on the DuPont schedule and its role in modern workforce management.
What is a DuPont Schedule?
The core principle behind the DuPont schedule is to provide a fixed work pattern that ensures continuous production while promoting employee well-being. Unlike traditional 8-hour or 10-hour shift schedules, which can be demanding for employees working extended hours, the DuPont schedule employs a 12-hour shift system. Here’s how it looks and typically works:
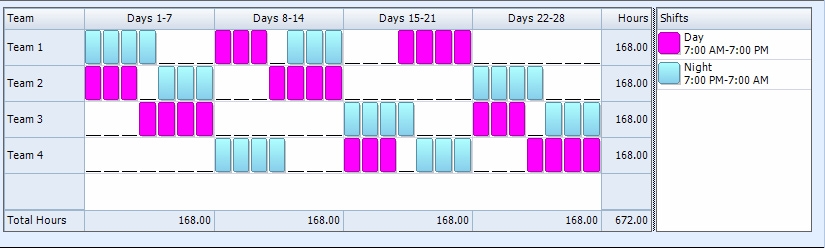
- 4 crews: The DuPont schedule divides the workforce into four crews, often referred to as “A,” “B,” “C,” and “D” shifts.
- 12-hour shifts: Employees work 12-hour shifts, allowing them to complete their weekly hours in fewer days than traditional 8-hour shifts. The most common rotation pattern is a combination of both day and night shifts.
- Rotating schedule: DuPont shifts follow a repeating pattern, often spanning a 28-day cycle. A common schedule is 4 days on (usually consisting of two-day shifts and two-night shifts) followed by 4 days off.
- Overtime mitigation: This schedule is designed to minimize overtime costs by utilizing a longer workday. Employees work fewer days each week but for more extended hours, reducing the need for additional overtime hours.
- Built-in rest: The schedule provides employees with extended days off, ensuring they have ample time for rest and personal life activities.
The DuPont shift work schedule is widely employed in industries that demand continuous production, such as petrochemical plants, healthcare scheduling, and utilities. While it offers advantages in terms of efficiency and reduced overtime costs, it also poses challenges, such as the potential for employee burnout due to long shifts and the need for effective shift handovers.
Shifts by Everhour provides an intuitive solution for managing employee schedules with ease. From flexible scheduling options to mobile accessibility, it’s the ideal solution for optimizing workforce management in any industry.
What is a Modified DuPont Schedule?
While the classic DuPont schedule is structured as a continuous 12-hour shift pattern, a modified version allows for alterations in shift lengths, rotations, or crew sizes. Here are some common modifications to the DuPont schedule:
⏳ Shift length variations: In a modified DuPont schedule, companies can choose to alter the length of shifts. Instead of strictly adhering to 12-hour shifts, they may implement 10-hour shifts or other variations to better align with employee preferences and fatigue management.
🔧 Rotational adjustments: The DuPont Schedule often follows a 28-day cycle, but organizations may modify this cycle to better suit their operational requirements. For example, they might implement a 21-day cycle or a 35-day cycle.
👨🤝👨🏼 Crew sizes: Depending on the workforce size and operational needs, the number of crews can be adjusted. While the classic DuPont schedule employs four crews (A, B, C, and D), a modified schedule may use more or fewer crews.
📣 Shift start times: Some organizations prefer to vary the start times of shifts within the DuPont schedule. This variation can help distribute the workload more evenly during peak production times.
🕗 Overtime management: Modifications may be made to better manage overtime costs. For example, organizations can implement policies that limit overtime on specific shifts or days.
The adaptability of the schedule is especially valuable in industries where production demands can vary significantly. By adjusting the DuPont schedule, organizations can strike a balance between continuous production, workforce satisfaction, and cost efficiency.
Sample DuPont Schedule for Small Businesses
Here is a sample DuPont schedule that you can use for your team.

Overtime Pay with the DuPont Schedule
Due to its 12-hour shift structure, employees often work fewer days per month compared to traditional 8-hour shift schedules, resulting in a reduced number of shifts that qualify for overtime pay. This feature is particularly attractive for organizations seeking to control labor costs while maintaining continuous operations. Here’s how the DuPont schedule for calculating overtime works:
😊 Fewer overtime-eligible days: With longer shifts, employees accumulate fewer overtime-eligible days per month. In a traditional 8-hour schedule, overtime may start after eight hours of work in a single day. In contrast, a 12-hour shift schedule may require employees to work up to 12 hours before overtime applies.
🕕 Overtime on rest days: Some DuPont schedules are designed to have built-in rest days between shifts, reducing the need for overtime on regular workdays. Employees can work longer hours on their shifts, which might include weekends, without exceeding weekly hour limits.
🔀 Shift rotation patterns: The DuPont schedule’s rotating pattern also contributes to overtime control. As shifts rotate between days and nights or among different crews, overtime hours can be distributed more evenly, minimizing the need for excessive overtime.
⚖️ Balanced workload: In industries with fluctuating workloads, the DuPont schedule allows organizations to adjust staffing levels and overtime requirements accordingly. During peak periods, shifts can be added or modified to accommodate increased production, and overtime can be strategically scheduled.
🤔 Labor cost predictability: The structured nature of the DuPont schedule makes labor costs more predictable for organizations. With fewer overtime-eligible days and controlled shift rotations, organizations can better manage labor expenses and budget accordingly.
However, it’s essential to note that while the DuPont schedule can reduce overtime costs, it may result in longer shifts for employees. Proper management and adherence to labor regulations are crucial to ensure employee well-being and compliance with overtime laws.
Who Uses the DuPont Shift Schedule?
The DuPont Shift Schedule, often referred to simply as the DuPont schedule, has found application across various industries due to its balanced approach to work hours. While not limited to these sectors, it is commonly used in the following fields:
🏭 Manufacturing: Manufacturers often adopt the DuPont schedule to maintain continuous production operations. The extended 12-hour shifts help minimize downtime between shifts, allowing facilities to operate around the clock more efficiently.
🛢️ Petrochemical and Refining: Industries involving the production of chemicals, petroleum products, and refining processes require constant monitoring and supervision. The DuPont schedule is suitable for these environments as it ensures adequate staffing for uninterrupted operations.
💉 Healthcare: Hospitals, clinics, and healthcare facilities use the DuPont schedule for their nursing staff and other critical healthcare roles. It helps ensure 24/7 coverage, reducing the need for frequent shift changes.
🚑 Emergency Services: Police, fire departments, and emergency medical services often employ the DuPont schedule. It provides consistent personnel availability for rapid response to emergencies.
⚡ Utilities: Energy production, water treatment plants, and utilities rely on the DuPont schedule to maintain essential services. It’s particularly valuable in ensuring uninterrupted power generation and water treatment.
⛏️ Mining: The mining industry, which operates in remote and demanding environments, benefits from the DuPont schedule’s extended shifts and continuous coverage.
🚌 Transportation: Some transportation companies, especially those involved in long-haul trucking and shipping, use the DuPont schedule to optimize driver schedules and maintain service levels.
🛫 Aerospace: Aircraft maintenance and airport operations often require round-the-clock staffing, making the DuPont schedule a suitable choice.
📞 Call centers: Customer service centers, telemarketing, helpdesk operations, and other enterprises that may require call center scheduling may utilize the DuPont schedule to ensure extended availability for customers.
🔐 Security: Security services, including manned security and surveillance operations, rely on this schedule to provide 24/7 protection.
✅ Advantages of DuPont Shift Schedules
The DuPont shift schedule, whether in its traditional form or as a modified version, offers several advantages to organizations and their employees. These advantages contribute to its popularity in industries that require continuous operations. Here are some key benefits:
- Continuous operations: DuPont schedules ensure that operations run continuously, 24/7, without the need for daily shift changes. This is particularly valuable in industries like manufacturing, healthcare, and public safety, where round-the-clock coverage is essential.
- Reduced overtime: By extending shifts to 12 hours, employees typically work fewer days per month. This leads to reduced overtime costs for organizations, as employees can often meet their weekly hour requirements within fewer days.
- More days off: Employees on a DuPont schedule often enjoy longer periods of time off between shifts. This extended break allows for a better work-life balance, which can lead to higher job satisfaction and lower turnover rates.
- Increased productivity: Longer shifts can result in increased productivity during work hours, as employees have fewer shift changes and less time spent transitioning between tasks.
- Lower turnover: Job satisfaction tends to be higher among employees on DuPont schedules due to the extended time off. This can lead to lower turnover rates, saving organizations time and money on recruiting and training.
- Predictable schedule: DuPont schedules are known for their predictability. Employees can plan their personal lives around their work schedules more easily, reducing scheduling conflicts.
- Employee preferences: Some employees prefer working longer shifts in exchange for more days off. DuPont schedules cater to these preferences, which can boost morale and motivation.
- Safety improvements: Longer shifts can result in fewer shift changes, reducing the likelihood of communication gaps or errors during handovers. This can enhance workplace safety, especially in high-risk environments.
- Environmental impact: Less commuting leads to reduced energy consumption & a smaller carbon footprint.
- Cost savings: Organizations often experience cost savings in terms of reduced overtime, improved productivity, and lower turnover, making the DuPont schedule an economically sound choice.
❌ Disadvantages of DuPont Shift Schedules
As with any shift schedule, the DuPont schedule has its share of disadvantages. While it offers several benefits, organizations should carefully consider these potential drawbacks before implementing it:
- Fatigue and burnout: Longer shifts, especially in high-intensity industries, can lead to employee fatigue and burnout over time. Maintaining focus and energy for 12 hours straight can be challenging, potentially affecting job performance and safety.
- Reduced family time: Although DuPont schedules provide more days off, longer workdays can limit the amount of time employees spend with their families. This can be a significant concern for those seeking work-life balance.
- Difficulty in shift coverage: Finding replacements for employees on extended shifts can be more challenging than traditional eight-hour shifts, potentially leading to scheduling conflicts.
- Safety concerns: While the extended work hours can enhance productivity, they can also pose safety concerns. Fatigued employees are more prone to errors and accidents, particularly in roles that demand high levels of concentration.
- Employee health: Extended shifts can take a toll on employee health, including increased risk of chronic conditions such as heart disease and diabetes. Additionally, maintaining a healthy lifestyle can be more challenging when working long hours.
- Resistance to change: Transitioning from traditional eight-hour shifts to DuPont schedules may face resistance from employees who are accustomed to the standard shift format. Managing this change effectively is crucial to a successful transition.
- Limited time for personal activities: Employees working 12-hour shifts often find themselves with limited time for personal activities, hobbies, and social engagements. This can impact their overall quality of life.
- Training requirements: Organizations may need to invest in additional training for employees to adapt to longer shifts.
- Administrative complexity: Managing a DuPont schedule can be more administratively complex than traditional schedules, particularly when dealing with shift swaps, time-off requests, and compliance with labor laws.
- Regulatory compliance: Depending on the industry and location, there may be specific labor regulations governing shift lengths and overtime pay that organizations must navigate when implementing DuPont schedules.
Are There Other 12-Hour Shift Schedules?
2-2-3 schedule
The 2-2-3 schedule consists of two days on, two days off, and a three-day weekend. It’s popular because it provides more consecutive days off, allowing employees to recharge. However, it may require more shift rotations, leading to scheduling complexities.
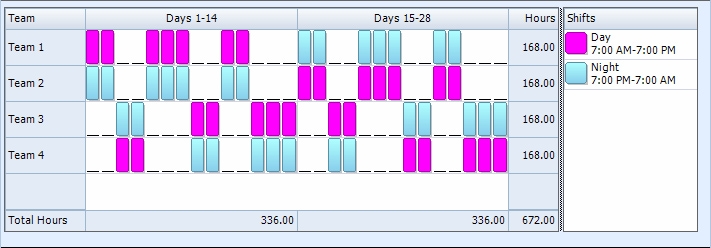
4-3 schedule
In this schedule, employees work four days in a row, followed by three consecutive days off. It’s often preferred for its longer weekends, making it suitable for those who prioritize extended breaks.
Panama schedule
The Panama schedule involves a mix of day and night shifts over a specific period, often with a set number of days on and days off. Industries requiring 24/7 operations, such as manufacturing and healthcare, usually are the ones employing this pattern.
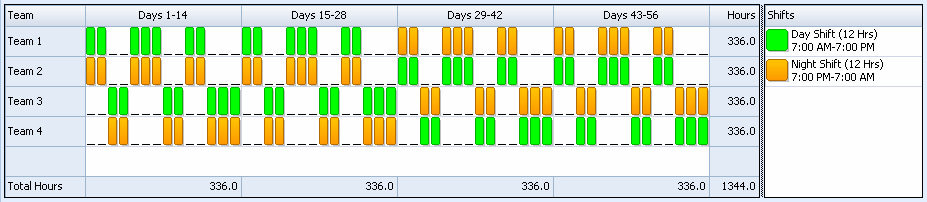
7-on, 7-off schedule
In this schedule, employees work seven consecutive days followed by seven days off. You can use this schedule type in healthcare, emergency services, and oil and gas industries.
2-2-4 schedule
This schedule features two days on, two days off, and four days on, followed by a series of days off. It offers longer breaks but may require more shift changes.
Custom schedules
Many organizations create custom 12-hour shift schedules tailored to their specific requirements. These schedules can include various combinations of days on and off, as well as different shift patterns.
DuPont Schedule: Conclusion
The DuPont schedule has been a valuable tool for organizations across various industries. Offering a balance between work and leisure time, it aims to enhance employee productivity and satisfaction while maintaining operational efficiency.
However, like any shift schedule, the DuPont schedule is not without its challenges. The complexity of managing multiple teams and shift rotations can pose logistical issues. It’s essential for organizations to carefully plan and monitor their schedules, taking into account the unique needs of their workforce.